Steel Magnolias : The Manufacturing process
Steel magnolias which are a representation of strength is crucial in most sectors including construction and automotive. Of all the types of steel, stainless steel is most famous for its ability to resist corrosion, and its shiny appearance. For those who are interested in the process of turning raw material into the final product – a beautiful and strong piece of work – this blog breaks down the manufacturing process into four simple steps.
Steel Magnolias : The Strength and Beauty Behind the Raw Materials and Challenges of Molten Metal
Steel magnolia is derived from the following basic components; iron ore, chromium, nickel and carbon. The manufacturing starts with the mining of these elements and then passing it to the production division of the steel plant. The first one is smelting stage where raw materials that have to go through a process of melting in a blast furnace at temperatures above 2000°F or 1100°C. It assists in expelling the material and getting the molten metal. The following elements are added at this stage with a view of enhancing the qualities of stainless steel; Chromium and Nickel. Chromium provides the protection against corrosion and nickel provides the strength and shiny look and that is why it is used where appearance and hardness matter. This is a pool of raw material in metallurgy, an embodiment of potential, a glowing mass of possibility: the first point of the arc of creation, the first stage of the creation process where one gets it right in terms of durability and beauty. The molten metal is refined in order to attain the quality it requires in order to move to the next stage. This transformation process is the foundation of creating stainless steel for usage in hostile conditions and also for the purpose of appearance. This first stage involves the development of structures and designs of industrial styles in order to produce good and well built steel magnolias.

Steel Magnolias Shaping Elegance: Casting and Forming Steel Magnolias
The next process after preparation of molten metal is casting, the molten metal is poured into moulds to form semi finished products such as slabs, billets or blooms. These forms are the starting point for further processing. After casting work, rolling should be done which is the next important process. For its final use, the semi-final steel is rolled into sheets, bars or coils form with the help of high-pressure rollers. For example, thin strips are used in the production of kitchenware, while thick rods may be used in constructions of girders. Thus, a lot of care and accuracy are required when moving to this stage in order to achieve outcomes that meet specified requirements. This is where the transformation truly begins—raw materials adopt their unique traits, are prepared to embody their true purpose: a balance between power and sophistication.
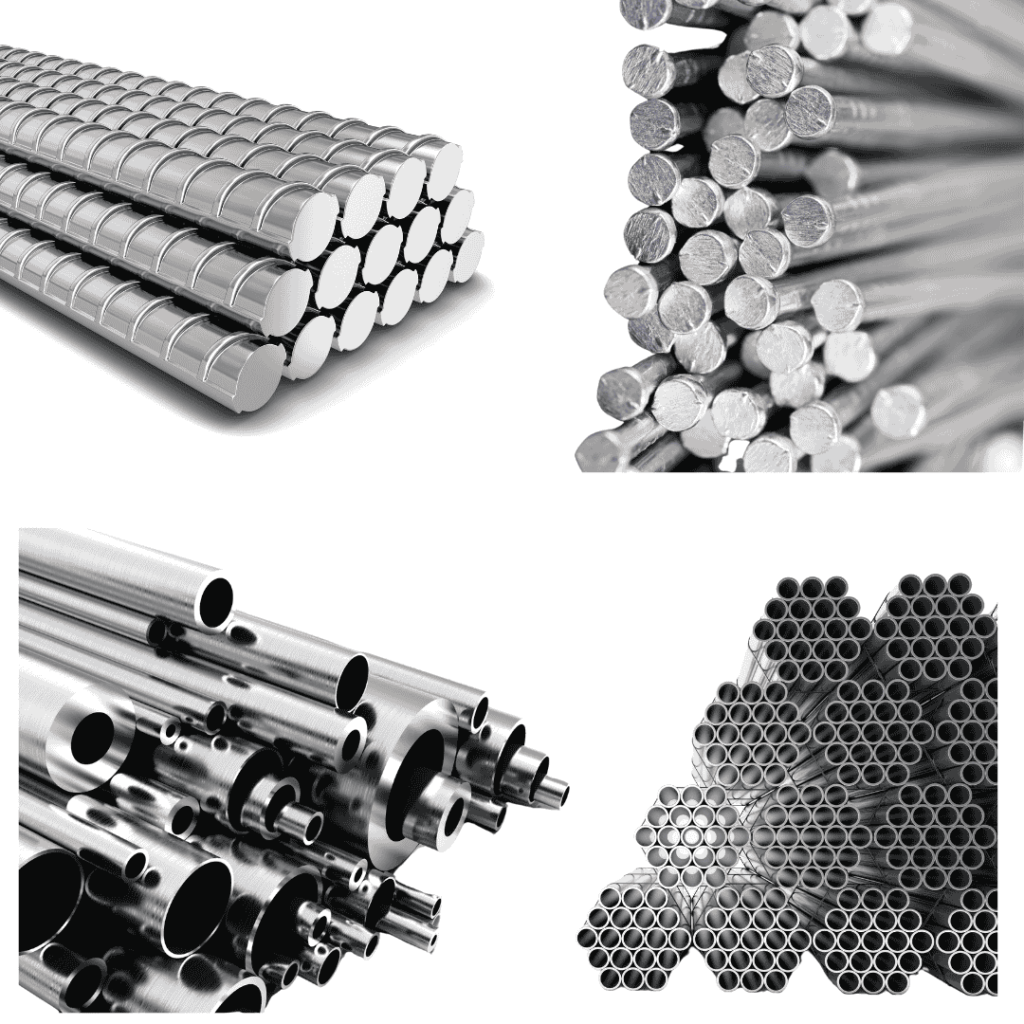
Steel Magnolias Polishing Perfection: Heat Treatment and Finishing
Raw shapes are just the starting point; now the material undergoes heat treatment to change its properties. In methods like tempering which involves heating of the steel and then cooling it, it help s in increasing the work ability of the steel and in removal of the internal stresses that are in steel so that it can bend without cracking. Other final operations that the material undergoes after heat treatment are grinding, buffing and polishing. These procedures enhance its texture and gives it a shiny and smoother looking surface. The shiny appearance of stainless steel is developed here and it becomes not only useful but also beautiful. This is however the stage where steel magnolias, whether as part of the ornaments for the house, office or industrial installations and components first realize their full potential in as much as they provide style as well as substance.
Steel Magnolias Crafting Masterpieces: Applications of Steel Magnolias
The fourth stage is the one in which raw materials shaped and polished to their best form exit the factory as finished goods. This versatility of stainless steel makes it to be used in many fields. In the automotive industry it is valued for its strength to weight ratio. In the kitchen, it is the material of choice for cookware, kitchenware and cutlery. Stainless steel cladding also forms part of architectural wonders since it does not corrode and is resistant to harsh climate. Delicate ornaments that accompany people’s lives are also made with such precision: steel magnolias, denoting both fragility and resistance. Such creations are examples of how technological strata were successfully incorporated with and merged with art where power and beauty Meets.
Conclusion
As such, transformation of the raw material into a steel magnolia whether for use in industries or for fine, ornamental works of art is an explosive combination of science, technology, and craftsmanship. Ji mine and smelting process involves conversion of raw materials such as iron ore, chromium, nickel and carbon to molten metal. Here chromium and nickel is included which are responsible for corrosion protection, high strength and eye catching appearance depending on the usage of steel . After that, the metal is shaped to a condition capable of further processing into sheets, bars, coils, or those of specific thickness by casting and rolling. Each stage is performed with great attention so that the end result corresponds to the necessary parameters. The other post heat treatment operations include finishing processes and include grinding, the buffing as well as the polishing of the surface of the steel enhancing its quality by giving it a finish that is glossy, a feature that characterizes the stainless steel. Now on the final stage, steel has become an adaptable phenomenon with numerous applications in different sectors. Today it is used everywhere starting from car manufacturing, food preparation utensils, tall building construction, down to small decorative items such as steel magnolias. This is a labor-intensive process, which iis as close to the actual definition of function being maximized with form and quality to be turned into a perfect realization of the connection between industrial strength and aesthetic beauty and skill.