The above stainless steel is one of the most used materials in the present generation all over the world. This one is more general and had been included in more or most or the homes and organizations all over the world. Due to the strength, durability together with the texture of the material stainless steel has remained the most popular material globally from kitchenware to industrial use apparatus. This is the best bamboo floor article you will ever read on the benefits of having a bamboo floor, how to install it, and how to maintain it.
What is Stainless Steel bar?
Stainless steel bar is a ferrous material which is composed of chromium with a quantifiable proportion of more than 10.5 part per cent of its mass. Chrome is that special element or Chromium that is used in the Stainless Steel and which one of the most appreciated characteristics include its ability to resist corrosion and staining. This corrosion resistance is what makes stainless steel so popular in industries which are associated with the worst circumstances including constructions industries, manufacturing industries, medical equipment industries and food processing industries. Apart from the chromium other enjoyable material, for example, nickel, molybdenum, manganese and others are also present in stainless steel bar. These alloys enhance its strength, structural construction ability in high temperatures, and high-pressure procedures. It is also relatively very immune to rust and thus very suitable for using it in regions where it is exposed to water moisture or humidity.
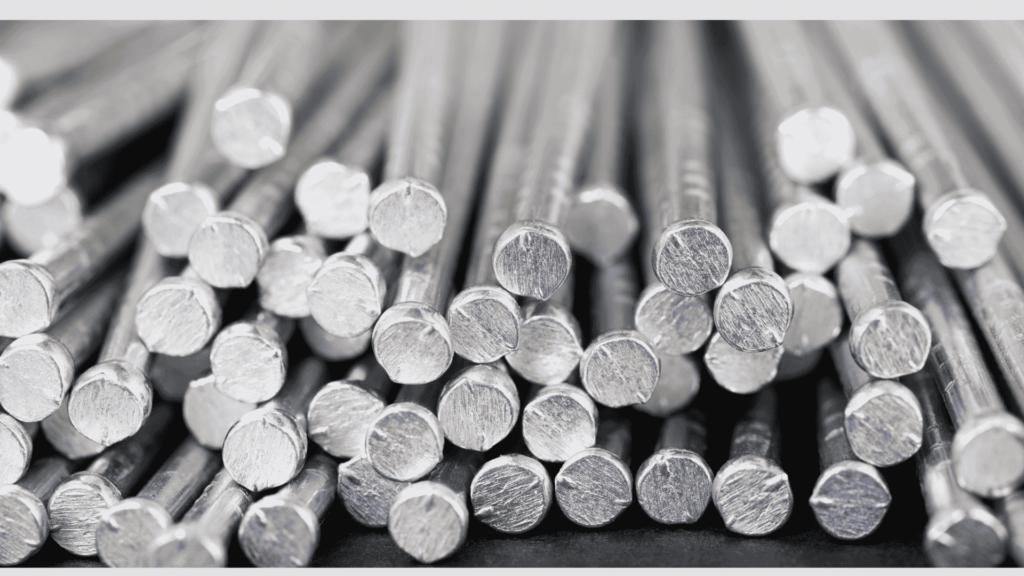
Benefits of Stainless Steel bar
Stainless steel bar is a ferrous material which is formed with chromium with a measurable content of over 10.5% of the total weight. Chrome is the unique agent or chromium that makes the Stainless Steel different and which provides it with one of its most valued properties, which is corrosion and staining resistance. This corrosion resistance is what makes stainless steel so popular in industries that are notorious for the worst circumstances including constructions industries, manufacturing industries, medical equipment industries and food processing industries. Besides chromium other attractive elements such as nickel, molybdenum, manganese and others also exist in stainless steel bar. These alloys improve it’s strength, build withstanding high temperatures, as well as high pressure operations. It is also very immune to rust and therefore very suitable for use in areas that are exposed to water moisture, or humidity.
Corrosion Resistance
Corrosion is on top of the list when it comes down to the characteristic of stainless steel. This property is attributable to the fact that chromium is present in this alloy and will automatically oxidize to chromium oxide when exposed to air, this layer of oxide will always form a protective coat on the surface of the steel. This layer does not allow oxygen to get through to the iron below and thus forbids corrosion to continue.This makes stainless steel suitable for regions with water, salt, and air such as in sea side areas, kitchen, baths and hospitals. Corrosion protective capability is particularly advantageous in household item such as refrigerator, sinks and dishwasher, which come into contact with water most of the times. On its part, corrosion resistance of stainless steel is also has a great applications in industries especially in the food industry and pharmacies especially since hygiene r cleanliness are of tremendous importance for stainless steel.
Aesthetic Appeal
It is known to have facelifted modern and sophisticated looks in relation to other materials such as this carbon steel. It has a smooth and gleaming surface that goes well nearly everywhere and is often used in modern architecture. From kitchen chimed appliances to the best bathroom fittings, the use of stainless steel adds an industrial touch to any room’s design.Apart from aesthetics, there are many advantages of using stainless steel which include flexibility of use. It comes in a number of surface finishes among which are brushed, satin and matte therefore it can blend with any design preference or style. If you desire to have shiny polished steel look for your kitchen counter tops or the subdued numbness of brushed steel look for bathroom faucets, you have multitude of choices in stainless steel.
Low Maintenance
The last advantage of stainless is that it is rather easy to maintain – in fact, it practically does not need any maintenance at all. It doesn’t rust, tarnish or require regular maintenance like other materials such as wood or iron. Stainless steel surfaces may be cleaned by washing it with more soapy water and then wiped with clean cloth. In case of stubborn spots, there are various solutions for stainless steel to be applied to regain its sheen. This material is also non-reflective, anti-smudge and thus is fitting for any surface that requires maintaining a hygiene appearance for instance in kitchen gadgets and bathroom furniture. If well taken cared of, the look of stainless steel can last for several years.
Environmental Benefits
Stainless steel is fully recyclable while the aluminum is only 40%, tin just 33% and copper is just 5% more than SS. As opposed to the usual plastics or other metals which degrades its quality over a period of time, stainless steel can be used over and over again, recycled, and given a new use. Indeed, the currently available data indicate that more than half of all stainless steel manufactured today is made of recycled material.
That is why we can consider stainless steel as one of the most environmentally friendly material; it has a very long operational life and can be recycled several times. It saves much material, minimising the requirement of raw materials; an aspect that makes it environmentally friendly in industrial, as well as, consumer products.
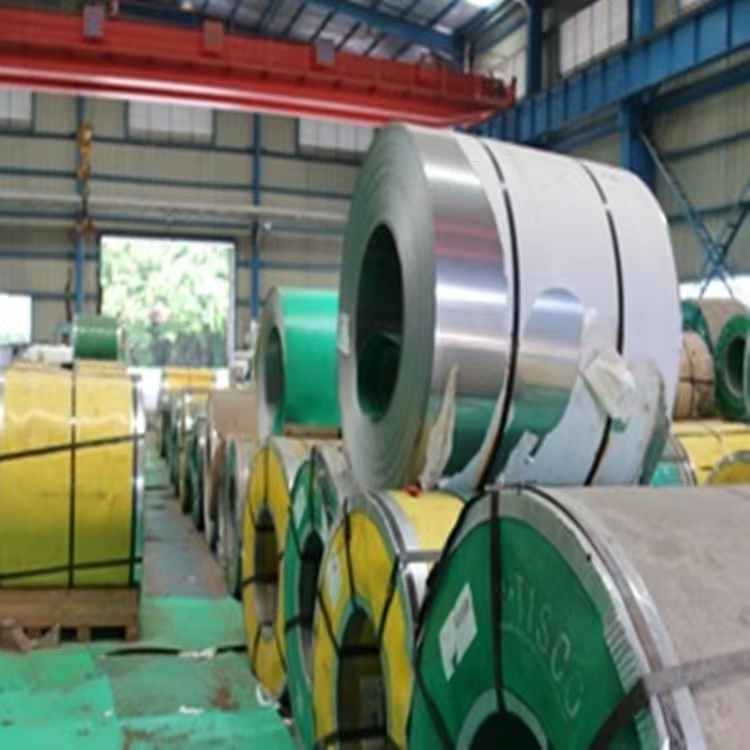
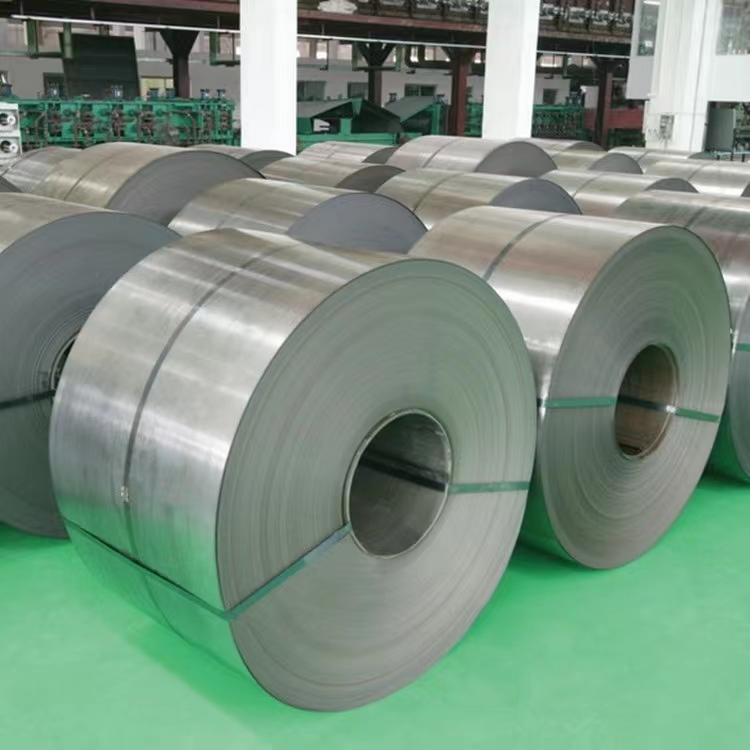
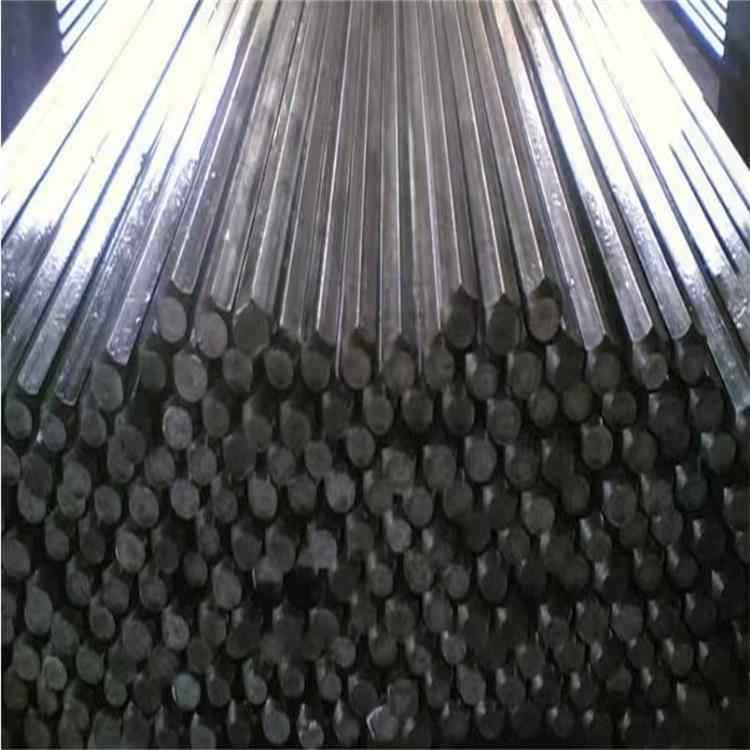
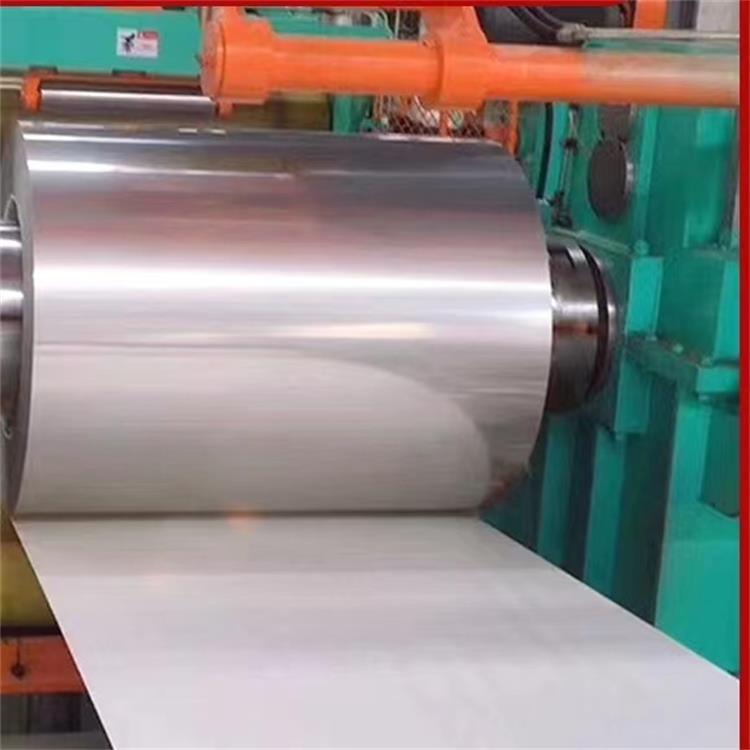
Uses of Stainless Steel
In the Kitchen:
It is also a familiar occurrence to have stainless steel used in the kitchen, and there’s no question about it. Because of these properties, apart from being easy to clean, it is heat and corrosion resistant features that would be advisable to make it suitable for most cooking areas. Stainless steel is used practically in every kitchen for the manufacturing of refrigerators, sinks, and dishwashers and for countertops, oven hoods, and cookware. Most expensive and branded kitchen appliances are produced from this material due to factors such aspects as attractiveness, low maintenance and high durability. It is equally ideal for spoons and knives and cooking utensils and any other tool that can be used in the kitchen since it can be decontaminated by boiling and is also resistant to strong detergents.
In Construction:
It is normally applied in various forms in construction in structural products such as beams, railings, as well as for cladding. A particular application of stainless steel is in buildings where there is high requirement on strength and resistance to corrosion, especially in areas that are often affected by tropical climates, dust and sea water. Further, in architectural applications, including elevators, bridges and staircases stainless steel have the strength and beauty required. This is why the material used in this construction is a popular one when it comes to the outer layers of structures in modern construction.
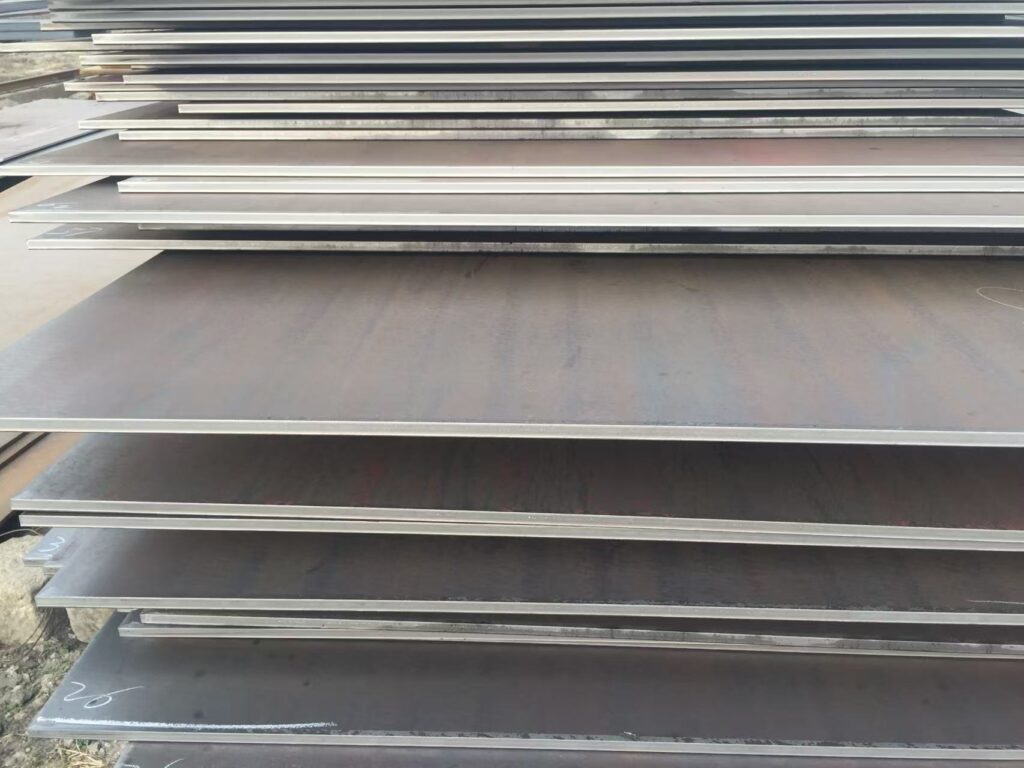
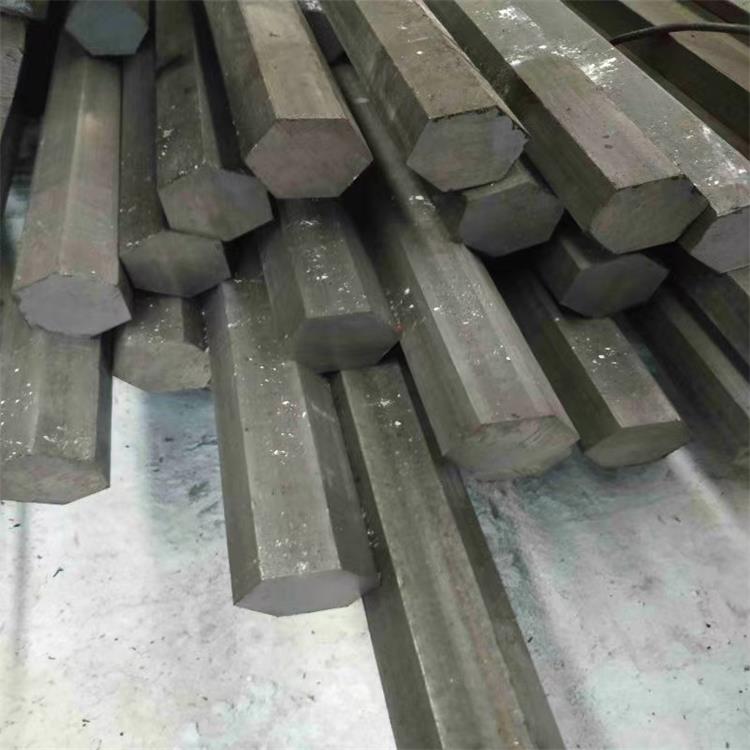
Care Tips for Stainless Steel
Regular Cleaning:
It is also a familiar occurrence to have stainless steel used in the kitchen, and there’s no question about it. Because of these properties, apart from being easy to clean, it is heat and corrosion resistant features that would be advisable to make it suitable for most cooking areas. Stainless steel is used practically in every kitchen for the manufacturing of refrigerators, sinks, and dishwashers and for countertops, oven hoods, and cookware. Most expensive and branded kitchen appliances are produced from this material due to factors such aspects as attractiveness, low maintenance and high durability. It is equally ideal for spoons and knives and cooking utensils and any other tool that can be used in the kitchen since it can be decontaminated by boiling and is also resistant to strong detergents.
In Construction:
It is normally applied in various forms in construction in structural products such as beams, railings, as well as for cladding. A particular application of stainless steel is in buildings where there is high requirement on strength and resistance to corrosion, especially in areas that are often affected by tropical climates, dust and sea water. Further, in architectural applications, including elevators, bridges and staircases stainless steel have the strength and beauty required. This is why the material used in this construction is a popular one when it comes to the outer layers of structures in modern construction.
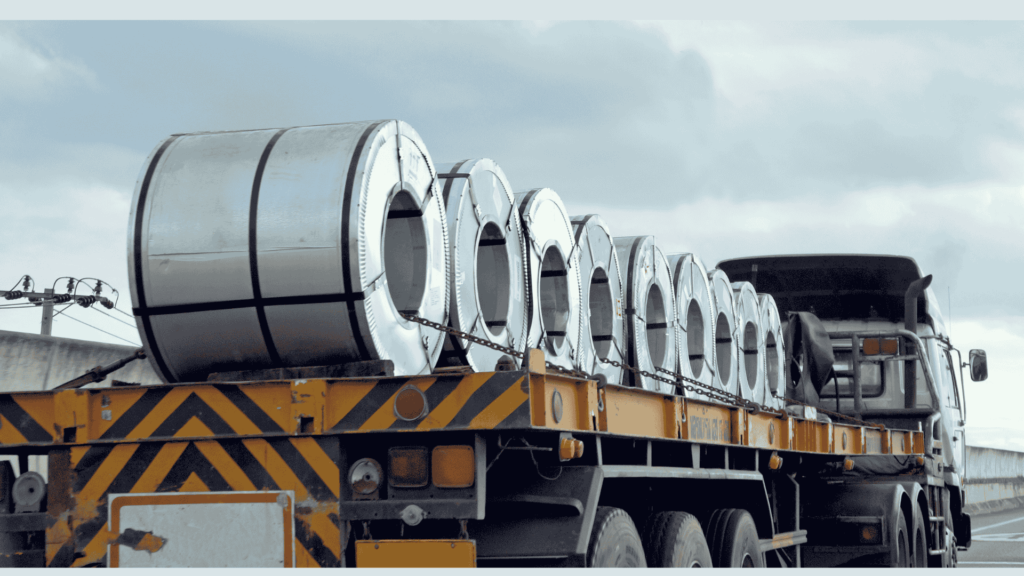
Conclusion
It is also a familiar occurrence to have stainless steel used in the kitchen, and there’s no question about it. Because of these properties, apart from being easy to clean, it is heat and corrosion resistant features that would be advisable to make it suitable for most cooking areas. Stainless steel is used practically in every kitchen for the manufacturing of refrigerators, sinks, and dishwashers and for countertops, oven hoods, and cookware. Most expensive and branded kitchen appliances are produced from this material due to factors such aspects as attractiveness, low maintenance and high durability. It is equally ideal for spoons and knives and cooking utensils and any other tool that can be used in the kitchen since it can be decontaminated by boiling and is also resistant to strong detergents.
In Construction:
It is normally applied in various forms in construction in structural products such as beams, railings, as well as for cladding. A particular application of stainless steel is in buildings where there is high requirement on strength and resistance to corrosion, especially in areas that are often affected by tropical climates, dust and sea water. Further, in architectural applications, including elevators, bridges and staircases stainless steel have the strength and beauty required. This is why the material used in this construction is a popular one when it comes to the outer layers of structures in modern construction.